The VAL working group is always interested in best practice examples from the world of logistics and innovative solutions are a perennial favorite. The visit to the IKEA logistics site in Dortmund was therefore a highlight this year. Christoph Dettmann, Central Fulfilment Unit Manager Deputy at IKEA Distribution Services GmbH & Co KG, and Marvin Jedlicka, Warehouse Manager, welcomed our group, gave a brief overview of IKEA’s supply chain and presented impressive figures right at the start. IKEA’s largest logistics unit in the world covers an area of around 135 hectares and is spread across several buildings. The 300 to 400 deliveries and removals by truck every day are moved in the huge halls by around 600 floor vehicles. 8.2 kilometers of conveyor technology are available. While the European Low Flow (ELF) and the High Flow (HF) supply the IKEA stores throughout Europe, the Customer Distribution Center (CDC) processes direct customer orders – for around 2,500 customers per day. The aim is to get the goods there in a maximum of 5 days. During an interesting tour of the CDC, our VAL working group was able to see how this can be achieved successfully. From goods receipt to dispatch, the group passed through various stations in the six individual hall sections. Incoming orders are split right at the beginning of the flow of goods: Boxes hold small parts, and picking is facilitated by the use of hand scanners. Larger items are picked by picking robots, which are designed to meet the requirements of furniture handling. The countless floor vehicles drive through the huge 23-meter-high silo in a one-way system. The central silo can store 61,000 Euro pallets. 100 to 110 pallet movements per hour are possible. The robotic picking system has 4 robot heads, all equipped with cameras. The robots pick the individual items according to previously learned packing patterns and bring them together for ordering. If required, pallets can be wrapped in film using two automatic wrapping machines. In the final quality assurance stage, the orders are checked before they are loaded onto trucks in the outgoing goods department. The VAL working group was able to inspect a perfectly integrated logistics system on site. It was particularly important for the group to be able to draw comparisons with their own logistics and to take away new ideas. Sustainable measures are particularly important in the shipping sector. This is why IKEA is increasingly dispensing with the use of wooden pallets where possible and is relying on metal platforms. Many of the returns go to the second chance market in the IKEA stores (formerly the “Fundgrube”), and mattresses are partially recycled. In addition, the space utilization of the trucks has been optimized by packing more mixed pallets and using length-adjusted transport trolleys. Communication is a top priority at the entire site: The “Pick-Nick” is available at central points and provides tips and recommendations on the individual work steps in several languages. Multilingual packing instructions and interpreter apps provide support. The conclusion for this informative afternoon: an all-round successful visit, which certainly gave many participants new ideas for logistics in their own company. NIRO would like to take this opportunity to thank Christoph Dettmann and Marvin Jedlicka for the exciting tour, the valuable insights into the world of logistics at IKEA and for patiently answering all interested questions!
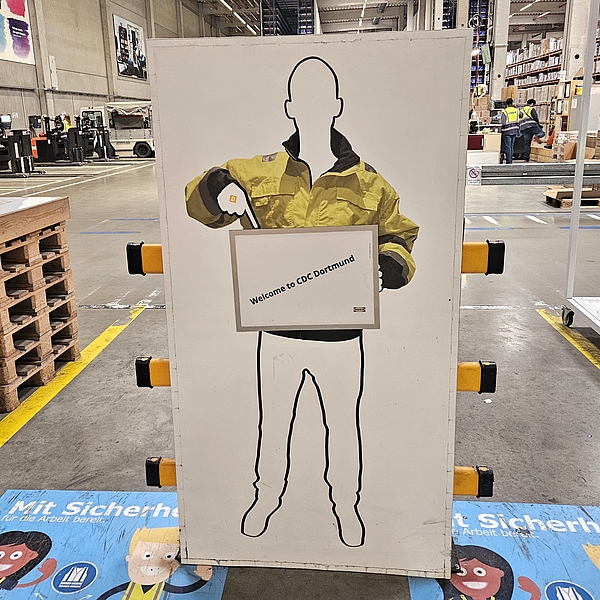