Die AG VAL bei uns ist immer interessiert an Best Practice-Beispielen aus der Welt der Logistik und innovative Lösungen sind ein Dauerbrenner. Der Besuch des IKEA Logistikstandorts in Dortmund war damit ein Höhepunkt in diesem Jahr.
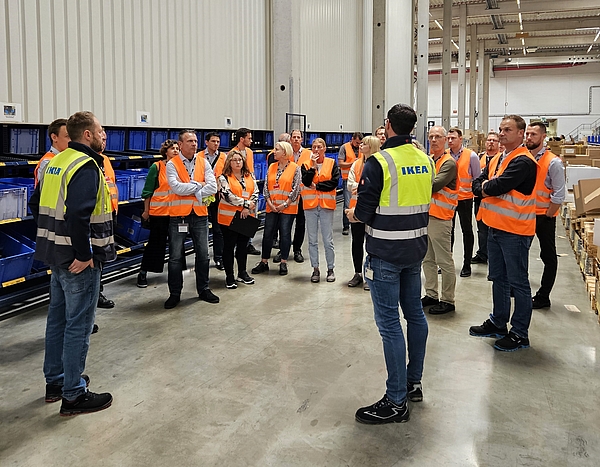
Christoph Dettmann, Central Fulfilment Unit Manager Deputy bei IKEA Distribution Services GmbH & Co. KG, und Marvin Jedlicka, Warehouse Manager, begrüßten unsere Gruppe, gaben einen kurzen Überblick über die Supply Chain von IKEA und präsentierten gleich zu Beginn beeindruckende Zahlen.
Die weltweit größte Logistikeinheit von IKEA nimmt eine Betriebsfläche von rund 135 Hektar ein und ist auf mehrere Gebäude verteilt. Die täglich 300 bis 400 An- und Ablieferungen von LKW werden in den riesigen Hallen von rund 600 Flurfahrzeugen bewegt. 8,2 Kilometer Fördertechnik stehen zur Verfügung. Während das European Low Flow (ELF) und das High Flow (HF) die IKEA Einrichtungshäuser europaweit beliefern, bearbeitet das Customer Distribution Center (CDC) die direkten Kundenbestellungen – für ca. 2.500 Kundinnen und Kunden pro Tag. Das Ziel: In maximal 5 Tagen soll die Ware dorthin gelangen.
Wie das erfolgreich gelingen kann, konnte unsere AG VAL bei einem interessanten Rundgang durch das CDC miterleben. Vom Wareneingang bis zum Versand durchlief die Gruppe unterschiedliche Stationen in den sechs einzelnen Hallenabschnitten.
Die eingehenden Bestellungen werden gleich zu Beginn des Warenflusses gesplittet: Boxen halten Kleinteile bereit, die Kommissionierung wird durch die Verwendung von Handscannern erleichtert. Größere Artikel werden von Pickrobotern zusammengestellt, die auf die Anforderungen des Möbelhandlings ausgerichtet sind.
Durch das 23 Meter hohe, riesige Silo fahren die unzähligen Flurfahrzeuge im Einbahnstraßensystem. Das zentrale Silo kann als Vorratslager 61.000 Europaletten unterbringen. 100 bis 110 Paletten-Bewegungen pro Stunde sind möglich.
Die Pick-Roboteranlage besitzt 4 Roboterköpfe, alle sind mit Kameras ausgerüstet. Nach zuvor erlernten Packmustern greifen die Roboter die einzelnen Artikel und führen sie zur Bestellung zusammen. Bei Bedarf können Paletten über zwei automatische Wickelmaschinen mit Folie eingepackt werden.
In der abschließenden Qualitätssicherung werden die Bestellungen überprüft, bevor sie im Warenausgang in LKW geladen werden.
Die AG VAL konnte ein perfekt ineinandergreifendes Logistik-System vor Ort in Augenschein nehmen.
Dabei war für die Gruppe besonders wichtig, Vergleiche zur eigenen Logistik ziehen zu können und neue Impulse mitzunehmen.
Gerade im Versandbereich sind nachhaltige Maßnahmen angesagt. Daher verzichtet IKEA zunehmend auf den Einsatz von Holzpaletten, wo es möglich ist, und setzt auf Metallplattformen. Viele der Retouren gehen in den Zweite-Chance-Markt der IKEA Stores (ehemals Fundgrube), Matratzen werden teilweise recycelt. Zudem wurde die Raumauslastung der LKW optimiert, indem mehr Mischpaletten gepackt werden und längenangepasste Transportschlitten eingesetzt werden.
Kommunikation wird am gesamten Standort groß geschrieben: An zentralen Punkten steht der „Pick-Nick“ bereit und gibt in mehreren Sprachen Tipps und Empfehlungen zu den einzelnen Arbeitsschritten. Mehrsprachige Packanweisungen und Dolmetscher-Apps unterstützen dabei.
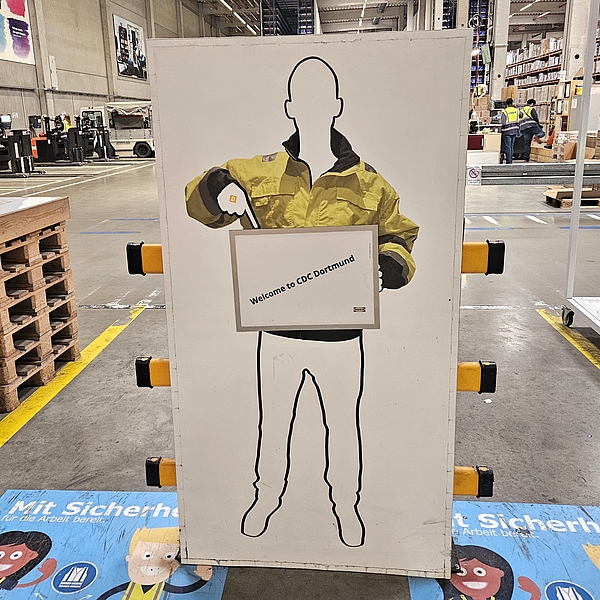
Das Fazit für diesen lehrreichen Nachmittag: ein rundum gelungener Besuch, der sicherlich für viele Teilnehmerinnen und Teilnehmer neue Ideen für die Logistik im eigenen Unternehmen mitbrachte.
NIRO dankt an dieser Stelle herzlich Christoph Dettmann und Marvin Jedlicka für die spannende Führung, die wertvollen Einblicke in die Logistikwelt von IKEA und die geduldige Beantwortung aller interessierten Fragen!